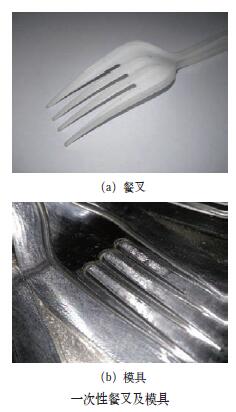
1.Application : For Motorcycle Accessories
2.Dimension: Customized dimension, OEM & ODM
3.Material: A6063, A6061, A3003 and other series alu alloy
4.Suface treatment: Anodizing, polishing, turning ,power coating, mill finish etc
5.Equipment: CNC ,extruding machine, cold drawn machine, heating oven, straightening machine, cutting machine
OD |
OD Tolerance |
ID Tolerance |
Roundness |
Straightness |
Circular run-out |
φ16-20 |
±0.02 |
±0.02 |
0.01↓ |
0.015↓ |
0.05↓ |
φ20-30 |
±0.02 |
±0.02 |
0.01↓ |
0.015↓ |
0.05↓ |
φ30-50 |
±0.05 |
±0.05 |
0.02↓ |
0.020↓ |
0.08↓ |
φ50-80 |
±0.15 |
±0.10 |
0.05↓ |
0.025↓ |
0.10↓ |
6. STANDARD PACKING:Wooden case/carton
7. Trade Terms
1. Payment: 30% T/T in advance, 70% balance pay before delivery. L/C at sight.
2. Delivery time: 20 days after deposit receiverd. If opening mould, plus 7-10 days.
3. Trade Term can be chosen depending on your requirements.
4. FOB Port: Shanghai
Extrusion Tube For Motorcycle Accessories
Extrusion Tube For Motorcycle Accessories,Motorcycle Parts Extrusion Tube,Aluminum Extrusion Tube For Motorcycle,Motorcycle Accessories Extrusion Tube
Changzhou YiFei Machinery Co., Ltd. , https://www.yifeialu.com