The sump gas collecting cover is usually made by hand-paste molding. Because the span of the cover is relatively large, the quality of the cover is very high, and the sump is generally large, so the cover of the same batch is required. There are also a large number of plates, which also requires that the interference of external factors must be minimized during the production process of the cover plate. The sump gas collecting cover is usually made by hand-paste molding. Because the span of the cover is relatively large, the quality of the cover is very high, and the sump is generally large, so the cover of the same batch is required. There are also a large number of plates, which also requires that the interference of external factors must be minimized during the production process of the cover plate.
The effluent cover is made of hand lay-up, because each employee's proficiency is different, even if the same employee is affected by external factors such as his emotion during the production process, this will result in many production processes in the cover. Variable factors directly affect the quality of the cover;
Secondly, the hand lay-up method is adopted. Because the cover plates are relatively large, the workplace is very chaotic. The ground is full of dripping resin, and the construction environment is difficult to control, which has a direct impact on the on-site production staff's mood and on-site production safety.
Finally, the hand lay-up method is adopted, because the cover plate will release the organic odor during solidification molding (Note: the VOC emission of the FRP open molding process exceeds 500 ppm, and the volatile amount of styrene is as high as 35%-45% of the use amount, and the regulations of each country Both are in the range of 50-100ppm; currently most of the foreign countries use cyclopentadiene (DCPD) or other low-styrene release resins, but styrene as a monomer is not a good substitute), there will be a certain environment around the production site. Hidden dangers are not conducive to the environmental protection that the country is advocating under the current situation.
In view of the requirements of the above cover plate and the problems existing in the hand lay-up method, our company has developed the vacuum inlet forming method of the sewage pool gas collecting cover by referring to the advanced FRP forming process at home and abroad, which can well solve the above hand lay-up method. There are problems. The vacuum resin introduction molding process is a low-cost manufacturing process developed in recent years, and is particularly suitable for the manufacture of large-scale products, and the advantages thereof are as follows:
(1) The product has excellent performance and high yield. In the case of the same raw material, the strength, rigidity and other physical properties of the vacuum resin introduction process molding member can be increased by 30% to 50% or more compared with the hand lay-up member; the yield can be close to 100% after the process is stabilized.
(2) The product quality is stable and the repeatability is good. Product quality is less affected by the operator, whether it is the same component or a high degree of consistency between the components. The fiber content of the product has been put into the mold according to the specified amount before the resin is injected. The component has a relatively constant resin ratio, generally 35%-45%, so the uniformity and repeatability of the product performance is better than the hand lay-up process product. More and fewer defects.
(3) The anti-fatigue performance is improved, and the structural weight can be reduced. Due to the high fiber content, low porosity, high product performance, especially the improvement of interlayer strength, the fatigue resistance of the product is greatly improved. Products made by the vacuum introduction process can reduce the structural weight when the strength or stiffness requirements are the same.
(4) Environmentally friendly. The vacuum resin introduction process is a closed mold process in which volatile organic compounds and toxic air pollutants are confined to a vacuum bag. There is only a trace amount of volatiles when the vacuum pump is vented (filterable) and the resin barrel is opened. VOC emissions do not exceed the standard of 5PPm. This has also greatly improved the working environment of the operators, stabilized the team of laborers, and expanded the range of materials available.
(5) The product is good overall. The vacuum resin introduction process can simultaneously form reinforcing ribs, sandwich structures and other inserts, which improves the integrity of the product, and thus can manufacture large products such as fan hoods, hulls and superstructures.
(6) Reduce the use of raw materials and reduce employment. When the same layer is applied, the amount of resin is reduced by 30%. Less waste, the resin loss rate is less than 5%. High labor productivity, saving more than 50% of labor compared to hand lay-up. Material and labor savings are even more impressive when forming large and complex geometries and reinforced structural members. For example, in the vertical rudder manufacturing of the aerospace industry, the reduction of fasteners by 365 is 75% lower than the conventional method, the weight of the product is unchanged, and the performance is better.
(7) The precision of the product is good. The dimensional accuracy (thickness) of the vacuum resin introduction process product is superior to that of the hand lay-up product. Under the same layup, the thickness of the general vacuum resin diffusion technology product is 2/3 of that of the hand lay-up product. The product thickness deviation is about 10%, and the hand lay-up process is generally 20%. The flatness of the surface of the product is better than that of the hand lay-up product. The inner cover of the hood product of the vacuum resin introduction process is smooth, and the surface naturally forms a resin-rich layer, and no additional top coat is required. Reduces the labor and materials used in the grinding and painting process.
Of course, the current vacuum resin introduction process also has certain disadvantages:
(1) The preparation process takes a long time and is complicated. Need to lay the right layer, lay the diversion medium, the draft tube, effective vacuum seal, etc. Therefore, for small-sized products, the process time is more than the hand lay-up process.
(2) The production cost is high and more waste is generated. Auxiliary materials such as vacuum bag film, flow guiding medium, release cloth and guiding tube are all used once, and at present, quite a lot of imports are dependent on, so the production cost is higher than the hand lay-up process. But the bigger the product, the smaller the difference. With the localization of auxiliary materials, this cost difference is getting smaller and smaller. The auxiliary materials that can be used multiple times in the current research are a development direction of the process.
(3) Process manufacturing has certain risks. Especially for large and complex structural products, once it fails in resin infusion, the product is easy to scrap. Therefore, there must be better preliminary research, strict process control and effective remedial measures to ensure the success of the process.
Sanding Sponge
The surface of the sponge sand is sand, which is sponge inside. It has super softness and is suitable for grinding any irregular geometric curved surface. It is better to take it at the same time. Applicable to all kinds of models doll hardware electronic furniture plastic artificial stone polishing and polishing sponge sand paper elastic grinding sponge with special sponge as the substrate, a layer of mineral sand on the outside, so that the product maintains the original grinding effect, more flexible, good to take and dry Wet dual-use characteristics. Can achieve twice the result with half the effort in the injection molding industry. It can handle slips on the surface of injection molded products, raw edges, and can also be polished.
kitchen nano emery magic clean rust removal sponge melamine sponge for a wide variety of curved, contoured or flat surface applications on wood, metal, paint, plastic, ceramics and drywall.the combination of flexible foam backing material and abrasive grit adhesion continually releases sanded material.Foam backing allows optimum pressure distribution to prevent sanding through surfaces,pressure spots are eliminated providing even surface pattern.Flexible foam allows adaptability to contours, shapes or areas of limited access,no folding or buckling results in an even pattern without scratching
We distributes and wholesales various brands of Bonded Abrasives , Abrasive Sanding Disc, Cutting Wheels , Flap Wheels , Flap Disc Backing Pad, Flap Disc Adhesive, and Surface Conditioning Product etc, and enjoy a high position among consumers.
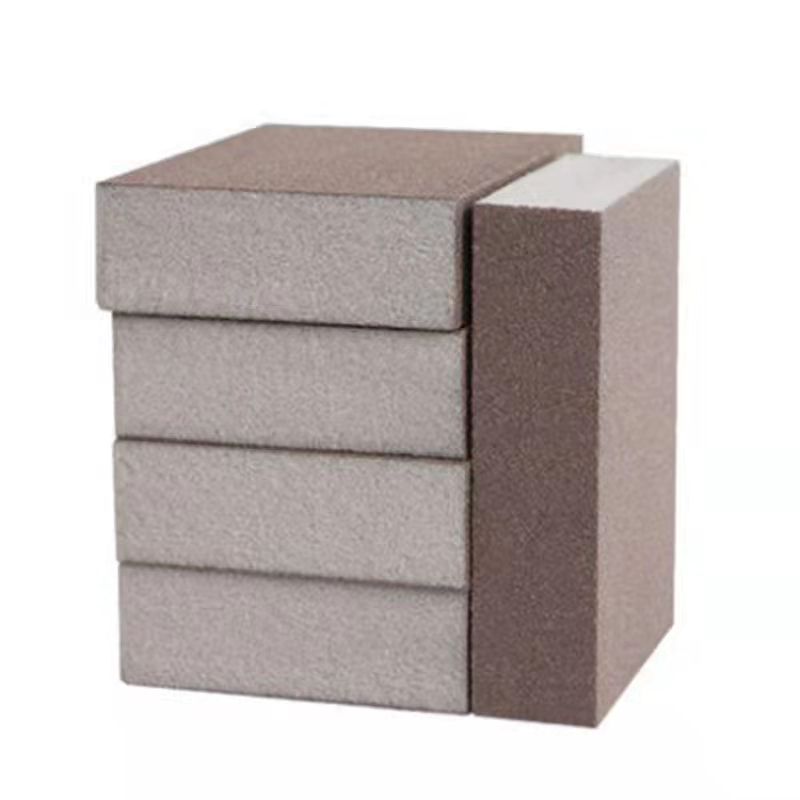
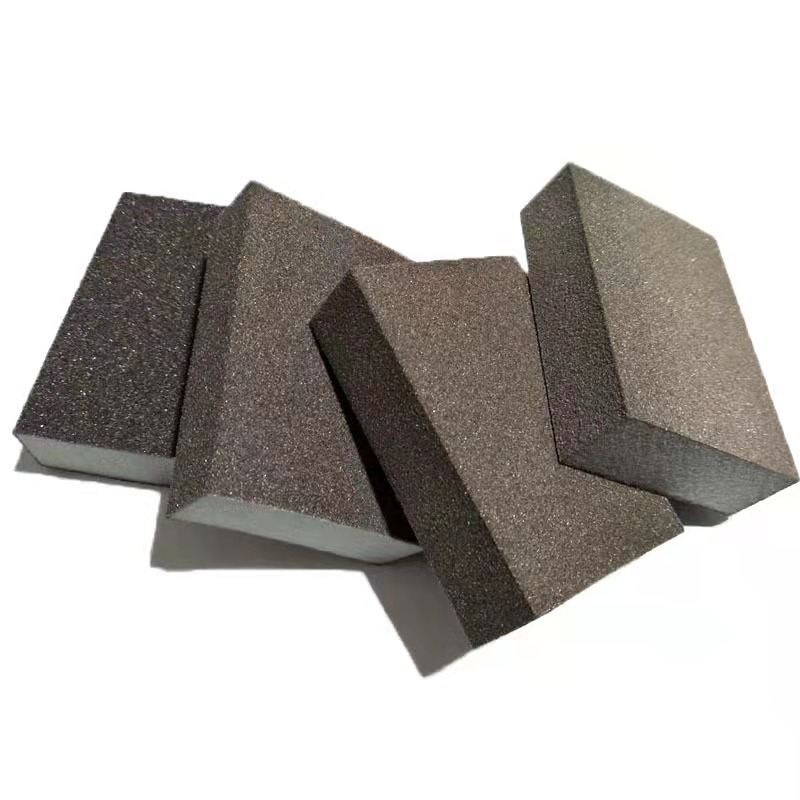

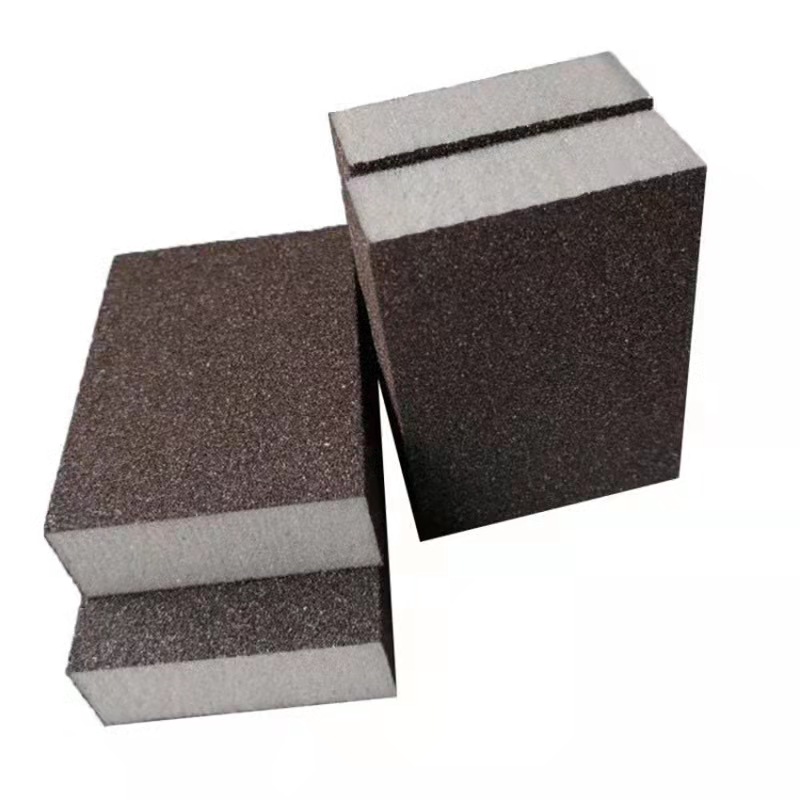
Sanding Sponge,Sanding Sponge Bunnings,Sponge Abrasive Pads,Gator Sanding Sponge
Zhengzhou Jiading Abrasive Manufacturing Co.,Ltd , https://www.jiadingabrasive.com