After the carburizing and quenching treatment of the large-size OG18 backstop inner ring of our company, after the inner hole end face of the finishing car and the grinding of the outer circular surface, cracks are generated during the process of cutting the inner hole keyway, resulting in the inner ring being scrapped, resulting in certain Economic loss. Through the analysis and explanation of the processing process of the inner ring process, this paper judges the cause of the cracking of the inner ring processing key groove and takes corresponding measures to avoid the failure of the key groove re-generation of the similar parts.
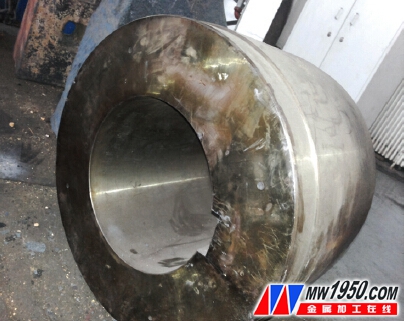
1. Inner ring keyway cracking description
The macroscopic shape of the inner ring is shown in Figure 1. The process flow is: forging blank → normalizing → roughing → carburizing → semi-finishing car (decarburizing layer) → quenching, tempering → finishing car → grinding outer circle → wire cutting keyway → Finished product. During the last process of inner ring machining, that is, the process of cutting the inner hole keyway, when the last face of the keyway is cut online, a crack occurs at the right angle of the bottom of the intersection with the previous machined surface, and extends to the end face (see Fig. 2, Fig. 2). 3). Cracks of the same state appeared in the inner ring of the same batch of 3 pieces, all of which were scrapped.
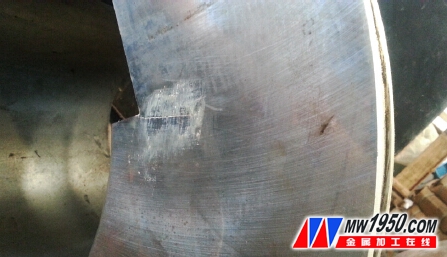
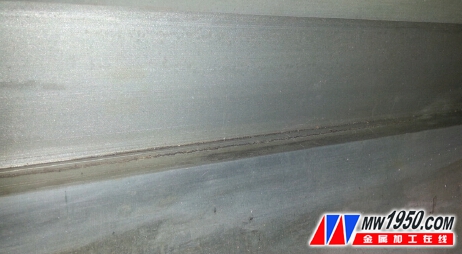
2. Discussion and analysis of the causes of cracks
The material of the inner ring of the backstop is 20CrMnMo. The technical requirements for the outer diameter of the outer circular surface are 90 to 62 HRC, and the hardened layer is 3 to 5 mm deep. Since the inner ring carburizing and quenching surface is a large-walled outer circular surface, it is quenched by a conventional oil cooling process, and the hardness of the carburized surface is only 45 to 50 HRC, which cannot meet the technical requirements.
For this purpose, the water-quenching oil-cooled two-liquid quenching process is adopted, and the quenching hardness of the outer surface of the carburized reaches the technical requirement lower limit of 57 to 58 HRC, and the hardness of the inner hole surface of the carburized layer is 40 to 50 HRC. Due to the high hardness of the inner hole surface, the subsequent keyway is processed by wire cutting. The first two batches of OG14 and OG16 small inner rings were quenched by the water quenching oil cooling process, and no cracking quality problems occurred after the wire-cut inner hole keyway was finished. OG14 inner ring contour size: φ490mm × φ240mm × 290mm, keyway length is 290mm; OG16 inner ring contour size is φ560mm × φ240mm × 360mm, keyway length is 360mm; and the OG18 inner ring contour size of the keyway cracking is φ640mm ×φ330mm×455mm, the length of the keyway is 455mm.
It can be seen that there is a large increase in the area of ​​the carburizing and quenching of the inner ring of the OG18 which has cracked and the size of the keyway. The larger the size of the processing keyway, the lower the strength of the base body, and the crack occurs when the last surface of the keyway is cut online, because the two faces of the keyway have been cut, which are stress-concentrated notches, resulting in a significant decrease in the strength of the substrate. When the stress is greater than the tensile strength of the substrate itself, cracking occurs. The stress causing cracking of the inner ring keyway is a superposition of various stresses, that is, residual stress after carburizing and quenching; machining stress of machining inner hole, end face and inner hole after quenching after carburizing; stress during wire cutting processing Wait.
Due to the large area and large wall thickness of the inner ring of OG18, the two-liquid quenching with water quenching oil cooling needs to increase the water cooling and oil cooling time, and strengthen the cooling, which will increase the residual stress after quenching; the inner ring size is more Larger, the more the semi-finishing machining such as carburizing after carburizing, the greater the cutting processing stress; the larger the inner ring keyway size, the greater the wire cutting stress. The base body has low strength and high stress, and is of course easy to crack. Larger composite residual stress and lower matrix strength are the main reasons for the cracking of the inner ring wire bond.
3. Improvement measures
For the remanufactured OG18 large-size inner ring assembly, adopt the process measures of reducing the comprehensive stress, that is, adding 2 to 3 times of long-term tempering on the basis of a tempering after the original process quenching, and then cutting the keyway to the finished product. There is no problem of keyway cracking and scrapping. Adopting the measures of strengthening tempering, increasing the number of tempering and tempering time after carburizing and quenching, so as to fully release the residual stress of carburizing, carburizing and quenching after processing, that is, reducing the comprehensiveness of the keyway when cutting Stress, which reduces the sensitivity of inner ring cracking.
4. Conclusion
(1) For the large inner ring, due to the large area of ​​carburizing and quenching and the increase of wall thickness, it is necessary to strengthen the cooling, so that the residual stress of carburizing and quenching increases; the size of the inner ring increases, and the amount of semi-finishing cutting increases. The machining stress is increased; the size of the keyway is increased, the wire cutting processing stress is increased, and the strength of the inner ring substrate is lowered. When the inner ring key groove is cut online, when the stress is greater than the strength of the base itself against brittle fracture, cracking occurs at the bottom of the inner ring key groove.
(2) After the inner ring is quenched, 2 to 3 times of long-term tempering; or semi-finishing after de-stressing treatment can reduce the comprehensive stress before the keyway processing, thereby reducing the sensitivity of cracking and avoiding the post-line cutting processing keyway. When there is a crack.
About the author: Zhao Wei, Liu Xiaorong, Li Wei, North Heavy Industry Group Co., Ltd.
Textured Roller,Wave Textured Paint Roller,Art Textured Paint Roller,Textured Foam Paint Roller
Jiangmen Nichiyo Decorative Material Co.,Ltd. , https://www.nichiyopt.com